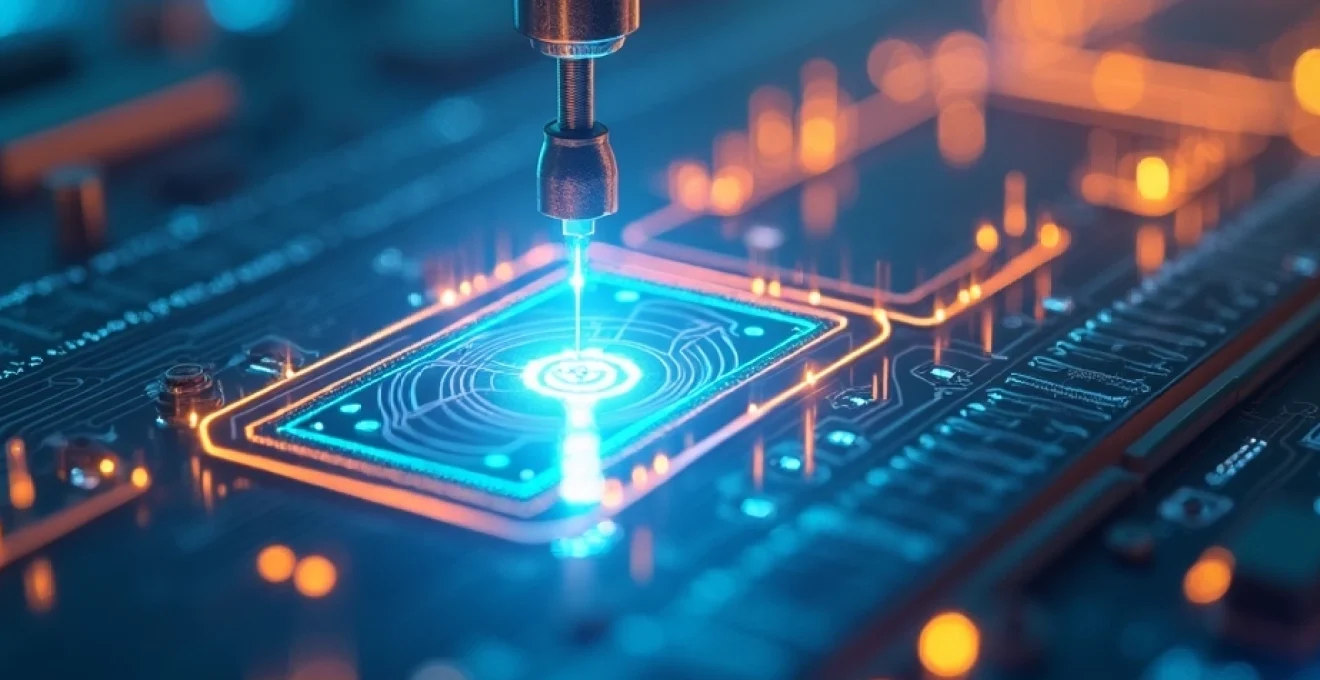
In today's rapidly evolving industrial landscape, technological advancements are revolutionizing productivity across various sectors. From artificial intelligence to cloud computing, these innovations are reshaping manufacturing processes, supply chains, and business operations. As industries embrace these cutting-edge technologies, they're experiencing unprecedented levels of efficiency, precision, and sustainability. Let's explore how these breakthroughs are transforming the way we produce goods and manage resources, ushering in a new era of enhanced industrial productivity.
AI-driven automation in manufacturing processes
Artificial Intelligence (AI) is at the forefront of the latest wave of industrial innovation, offering unprecedented capabilities in automating and optimizing manufacturing processes. By leveraging machine learning algorithms and sophisticated data analysis, AI systems are dramatically enhancing efficiency, reducing errors, and increasing overall productivity in factories worldwide.
Machine learning algorithms for predictive maintenance
One of the most impactful applications of AI in manufacturing is predictive maintenance. By analyzing vast amounts of sensor data from equipment, machine learning algorithms can predict when machinery is likely to fail or require maintenance. This proactive approach significantly reduces downtime and maintenance costs, ensuring that production lines run smoothly and efficiently.
For example, a large automotive manufacturer implemented an AI-driven predictive maintenance system that reduced unplanned downtime by 20% and maintenance costs by 15%. The system continuously monitors equipment performance, identifying subtle patterns that indicate potential issues before they become critical problems.
Computer vision systems for quality control
Computer vision, a subset of AI, is revolutionizing quality control processes in manufacturing. These systems use cameras and sophisticated image processing algorithms to inspect products at speeds and levels of accuracy that far surpass human capabilities. By detecting defects that might be invisible to the naked eye, computer vision systems ensure higher product quality and reduce waste.
A leading electronics manufacturer recently integrated a computer vision system into their production line, resulting in a 35% reduction in defective products reaching customers and a 25% increase in overall production efficiency. The system can inspect thousands of circuit boards per hour, identifying even the tiniest soldering defects or misaligned components.
Natural language processing in human-robot collaboration
Natural Language Processing (NLP) is enhancing communication between humans and robots on the factory floor. This technology allows workers to interact with robotic systems using voice commands and natural language, streamlining operations and reducing the learning curve for new employees working alongside automated systems.
A major automotive plant has implemented NLP-enabled cobots (collaborative robots) that can understand and respond to verbal instructions from human workers. This has led to a 30% increase in production speed and a 40% reduction in training time for new employees working with robotic systems.
Reinforcement learning for adaptive production scheduling
Reinforcement learning, an advanced AI technique, is being applied to optimize production scheduling in real-time. These systems can adapt to changing conditions, such as supply chain disruptions or fluctuating demand, to maintain optimal production efficiency.
A large consumer goods manufacturer has deployed a reinforcement learning system for production scheduling, resulting in a 15% increase in overall equipment effectiveness (OEE) and a 10% reduction in inventory costs. The system continuously adjusts production schedules based on real-time data, ensuring maximum efficiency and responsiveness to market demands.
Cloud computing and edge technologies in industrial IoT
The integration of cloud computing and edge technologies with the Industrial Internet of Things (IIoT) is creating a new paradigm for data processing and analysis in manufacturing environments. This convergence allows for more efficient data management, faster decision-making, and improved overall system performance.
5G networks enabling real-time data processing
The rollout of 5G networks is a game-changer for industrial IoT applications. With its high-speed, low-latency capabilities, 5G enables real-time data processing and communication between devices, robots, and central control systems. This ultra-fast connectivity is crucial for applications that require instantaneous decision-making, such as autonomous vehicles in warehouses or safety systems in hazardous environments.
A major logistics company has implemented a 5G-powered smart warehouse system, resulting in a 40% increase in picking efficiency and a 30% reduction in inventory errors. The system uses real-time location tracking and AI-powered routing algorithms to optimize the movement of goods and workers within the facility.
Fog computing architecture for latency-sensitive applications
Fog computing, an extension of cloud computing, brings data processing closer to the edge devices where data is generated. This architecture is particularly beneficial for latency-sensitive applications in manufacturing, such as real-time quality control or safety systems.
A semiconductor manufacturer has implemented a fog computing architecture in their clean room environment, reducing response times for critical process control decisions by 60% and improving overall yield by 8%. The system processes sensitive data locally, ensuring rapid responses to any deviations in the manufacturing process.
Blockchain for secure supply chain management
Blockchain technology is revolutionizing supply chain management by providing a secure, transparent, and immutable record of transactions and product movements. This technology enhances traceability, reduces fraud, and improves overall supply chain efficiency.
A global food distributor has implemented a blockchain-based supply chain management system, resulting in a 25% reduction in product recalls and a 20% increase in customer trust. The system provides end-to-end visibility of the supply chain, allowing for rapid identification of the source of any quality issues.
Digital twin technology for virtual process optimization
Digital twin technology creates virtual replicas of physical assets, processes, or systems. These digital models can be used to simulate and optimize manufacturing processes, predict maintenance needs, and test new configurations without disrupting actual production.
An aerospace manufacturer has implemented digital twin technology for engine design and production, reducing development time by 30% and maintenance costs by 25%. The digital twin allows engineers to simulate various operating conditions and optimize designs before physical prototyping, significantly streamlining the development process.
Advanced robotics and cobots in assembly lines
The latest advancements in robotics, particularly in the field of collaborative robots (cobots), are transforming assembly lines across industries. These sophisticated machines are enhancing productivity, improving worker safety, and enabling more flexible manufacturing processes.
Soft robotics for delicate material handling
Soft robotics represents a significant leap forward in the handling of delicate or irregularly shaped objects. Unlike traditional rigid robots, soft robots use flexible materials and pneumatic or hydraulic actuators to gently manipulate objects without damaging them.
A fruit packaging company has implemented soft robotic grippers in their sorting and packaging lines, increasing handling speed by 40% while reducing product damage by 30%. The soft grippers can adapt to various fruit shapes and sizes, ensuring gentle handling of even the most delicate produce.
Exoskeletons enhancing worker ergonomics
Exoskeletons are wearable robotic devices that augment human physical capabilities. In manufacturing settings, these devices can significantly reduce worker fatigue and the risk of repetitive strain injuries, particularly in tasks involving heavy lifting or repetitive motions.
An automotive assembly plant has equipped workers with upper-body exoskeletons, resulting in a 50% reduction in shoulder injuries and a 20% increase in productivity for overhead assembly tasks. The exoskeletons provide support and redistribute the weight of tools and components, allowing workers to perform tasks with less strain and fatigue.
Computer numerical control (CNC) advancements
CNC technology continues to evolve, with the latest advancements focusing on multi-axis machining, increased precision, and integration with AI for optimized toolpaths. These improvements are enabling the production of increasingly complex parts with higher accuracy and efficiency.
A precision engineering firm has upgraded to a 5-axis CNC machine with AI-optimized toolpaths, reducing machining time by 35% and improving part accuracy by 20%. The system's ability to machine complex geometries in a single setup has significantly streamlined the production process for high-precision components.
Autonomous mobile robots (AMRs) in warehousing
Autonomous Mobile Robots (AMRs) are revolutionizing warehouse operations by automating material transport and inventory management tasks. These intelligent robots can navigate complex warehouse environments, adapt to changing layouts, and work alongside human workers safely and efficiently.
A large e-commerce fulfillment center has deployed a fleet of AMRs, resulting in a 60% reduction in order picking time and a 40% increase in warehouse space utilization. The robots work collaboratively with human pickers, bringing shelves to packing stations and optimizing the use of vertical space in the warehouse.
Data analytics and business intelligence tools
The power of data analytics and business intelligence (BI) tools is transforming decision-making processes across industries. By harnessing the vast amounts of data generated in modern manufacturing environments, companies can gain unprecedented insights into their operations, leading to more informed strategies and improved productivity.
Big data platforms for production insights
Big data platforms are essential for collecting, processing, and analyzing the enormous volumes of data generated by industrial IoT devices, production equipment, and business systems. These platforms enable manufacturers to identify patterns, trends, and anomalies that can lead to significant productivity improvements.
A chemical manufacturing company implemented a big data analytics platform, resulting in a 15% increase in overall equipment effectiveness (OEE) and a 10% reduction in energy consumption. The platform analyzes data from thousands of sensors across the plant, identifying opportunities for process optimization and predictive maintenance.
Augmented analytics with natural language querying
Augmented analytics combines AI and natural language processing to make data analysis more accessible to non-technical users. This technology allows employees at all levels to query complex datasets using natural language, democratizing access to valuable business insights.
A consumer goods manufacturer has implemented an augmented analytics platform with natural language querying capabilities, leading to a 30% reduction in time spent on report generation and a 25% increase in data-driven decision making across departments. The system enables managers to quickly analyze sales trends, inventory levels, and production efficiency without relying on dedicated data analysts.
Prescriptive analytics for decision support systems
Prescriptive analytics takes data analysis a step further by not only predicting what might happen but also suggesting actions to optimize outcomes. These advanced systems use machine learning algorithms to provide actionable recommendations for improving productivity and efficiency.
An oil and gas company has deployed a prescriptive analytics system for its drilling operations, resulting in a 20% increase in well productivity and a 15% reduction in drilling costs. The system analyzes real-time drilling data, historical performance, and geological information to recommend optimal drilling parameters and strategies.
Additive manufacturing and 3D printing innovations
Additive manufacturing, commonly known as 3D printing, continues to evolve rapidly, offering new possibilities for product design, prototyping, and production. The latest innovations in this field are enabling faster, more precise, and more versatile manufacturing processes.
Multi-material 3D printing for complex components
Multi-material 3D printing technologies allow for the creation of complex components with varying material properties in a single print job. This capability is particularly valuable in industries such as aerospace and medical devices, where components often require a combination of different materials for optimal performance.
A medical device manufacturer has implemented multi-material 3D printing for producing customized prosthetics, reducing production time by 50% and improving patient satisfaction by 30%. The technology allows for the integration of rigid and flexible materials within the same prosthetic, enhancing comfort and functionality.
Large-scale additive manufacturing for industrial applications
Advancements in large-scale additive manufacturing are enabling the production of significantly larger components, opening up new possibilities for industries such as construction and automotive manufacturing. These systems can print large structures or parts in a fraction of the time required by traditional manufacturing methods.
A construction company has adopted large-scale 3D printing technology for building affordable housing, reducing construction time by 70% and labor costs by 50%. The system can print the basic structure of a small house in less than 24 hours, significantly accelerating the construction process.
4D printing for Self-Assembling structures
4D printing represents the cutting edge of additive manufacturing technology. This innovative approach involves printing materials that can change shape or properties over time in response to external stimuli such as heat, moisture, or light. The potential applications for this technology range from self-assembling furniture to adaptive medical implants.
A research institute has developed 4D-printed smart textiles that can adapt to environmental conditions, with potential applications in sportswear and protective clothing. These materials can change their structure to provide increased ventilation in hot conditions or enhanced insulation in cold environments, offering a new level of comfort and functionality.
Sustainable technologies for green manufacturing
As industries strive to reduce their environmental impact, sustainable technologies are becoming increasingly important in manufacturing processes. These innovations not only contribute to a greener planet but often lead to significant cost savings and improved efficiency.
Energy harvesting systems in smart factories
Energy harvesting technologies capture and utilize ambient energy sources such as vibrations, heat, or light to power sensors and other low-power devices in manufacturing environments. This approach reduces the need for batteries or wired power connections, making it easier to deploy IoT devices throughout a factory.
A smart factory has implemented vibration-based energy harvesting systems to power its network of condition monitoring sensors, eliminating the need for battery replacements and reducing maintenance costs by 40%. The self-powered sensors continuously monitor equipment health, contributing to improved predictive maintenance strategies.
Closed-loop recycling processes for zero waste
Closed-loop recycling processes aim to create a circular economy within manufacturing, where waste materials are recycled and reused in the production of new products. This approach not only reduces environmental impact but can also lead to significant cost savings in raw material procurement.
An electronics manufacturer has implemented a closed-loop recycling system for plastic components, reducing virgin plastic use by 60% and lowering material costs by 25%. The system recycles and reprocesses plastic waste from the production line, turning it into high-quality material for new product components.
Biofabrication techniques for eco-friendly materials
Biofabrication involves using living organisms or biological processes to produce materials and products. This emerging field offers the potential for creating sustainable, biodegradable alternatives to traditional manufacturing materials.
A packaging company has developed a biofabricated alternative to plastic packaging using mycelium (fungal roots), reducing plastic waste by 80% and energy consumption in production by 40%. The mycelium-based packaging is fully biodegradable and can be grown to exact specifications, eliminating the need for cutting or molding in the production process.
As these technological advances continue to drive significant improvements in productivity across industries, it's clear that we're entering a new era of manufacturing efficiency and sustainability. By embracing these innovations, companies can not only boost their productivity but also contribute to a more sustainable and environmentally friendly industrial future.