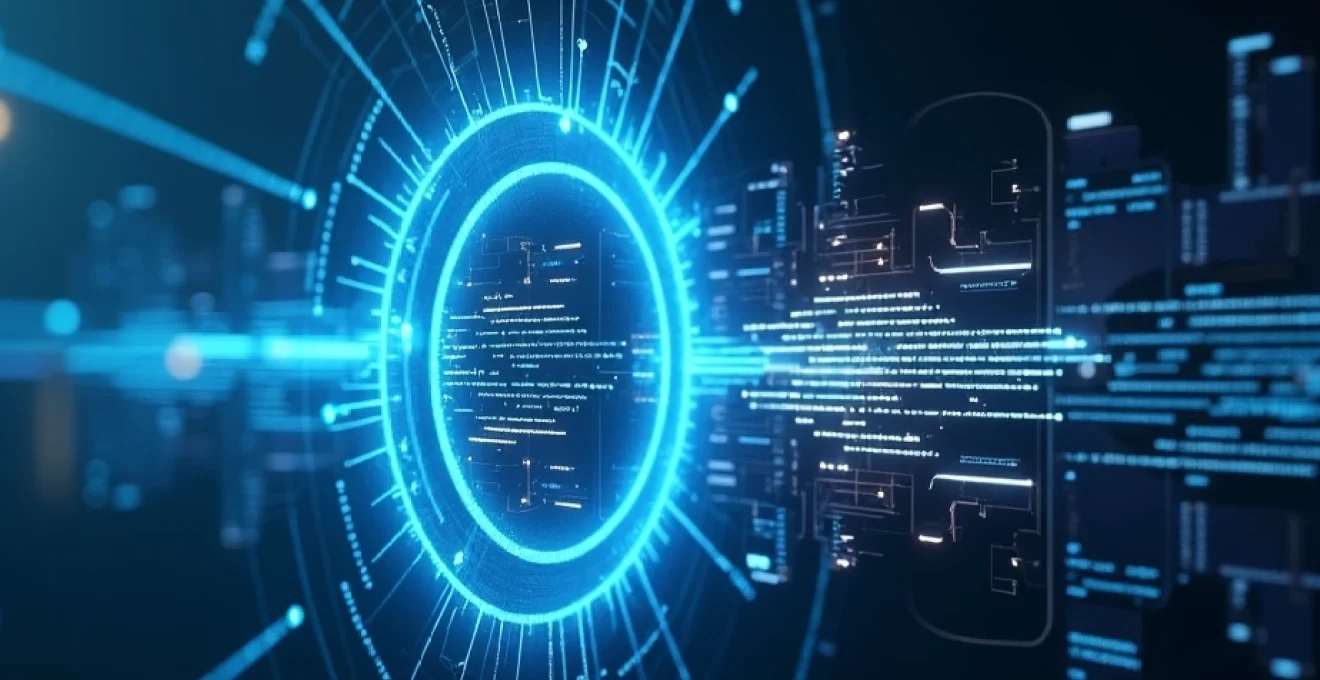
Developing an effective maintenance routine is crucial for maximizing equipment longevity, reducing downtime, and optimizing operational efficiency. In today's rapidly evolving industrial landscape, organizations must adopt a proactive approach to maintenance, leveraging cutting-edge technologies and best practices. By implementing a comprehensive maintenance strategy, businesses can significantly reduce repair costs, improve safety, and enhance overall productivity.
Preventive maintenance strategies for equipment longevity
Preventive maintenance forms the backbone of any effective maintenance routine. This proactive approach involves regularly scheduled inspections, cleaning, lubrication, and minor repairs to prevent unexpected breakdowns and extend equipment life. By addressing potential issues before they escalate, organizations can avoid costly emergency repairs and minimize production disruptions.
One key aspect of preventive maintenance is creating a detailed checklist for each piece of equipment. This checklist should include specific tasks, required tools, and estimated time for completion. Regular review and updates of these checklists ensure that maintenance procedures remain relevant and effective as equipment ages or operating conditions change.
Another critical component of preventive maintenance is proper documentation. Maintaining accurate records of all maintenance activities, including dates, technicians involved, and observations, provides valuable insights for future planning and troubleshooting. This historical data can help identify recurring issues and guide decisions on equipment replacement or upgrades.
Predictive maintenance techniques using IoT and machine learning
While preventive maintenance is essential, predictive maintenance takes equipment care to the next level. By leveraging Internet of Things (IoT) sensors and advanced machine learning algorithms, organizations can monitor equipment performance in real-time and predict potential failures before they occur. This data-driven approach allows for more precise maintenance scheduling, reducing unnecessary downtime and optimizing resource allocation.
Implementing vibration analysis for early fault detection
Vibration analysis is a powerful predictive maintenance technique, particularly effective for rotating machinery. By continuously monitoring vibration patterns, maintenance teams can detect subtle changes that may indicate impending failures. Advanced sensors and data analysis software can identify issues such as bearing wear, misalignment, or imbalance, allowing for timely intervention.
To implement vibration analysis effectively, consider the following steps:
- Install vibration sensors on critical equipment components
- Establish baseline vibration signatures for normal operation
- Configure alert thresholds for abnormal vibration patterns
- Integrate vibration data with your maintenance management system
- Train maintenance personnel on interpreting vibration analysis results
Leveraging thermography in HVAC system maintenance
Thermography, or thermal imaging, is an invaluable tool for maintaining HVAC systems and electrical equipment. By detecting temperature variations, maintenance teams can identify potential issues such as overheating components, insulation failures, or refrigerant leaks. Regular thermal inspections can prevent costly breakdowns and improve energy efficiency.
When incorporating thermography into your maintenance routine, consider these best practices:
- Conduct thermal scans during peak load conditions for accurate results
- Establish temperature thresholds for different equipment types
- Use high-resolution thermal cameras for precise measurements
- Maintain a database of thermal images for trend analysis
Oil analysis: tracking equipment health through lubricant monitoring
Oil analysis is a critical predictive maintenance technique for equipment with lubricating systems. By regularly sampling and analyzing oil, maintenance teams can gain valuable insights into equipment health, including wear rates, contamination levels, and potential component failures. This technique is particularly useful for engines, gearboxes, and hydraulic systems.
To implement an effective oil analysis program:
- Establish a consistent sampling schedule for each piece of equipment
- Use proper sampling techniques to ensure accurate results
- Partner with a reputable laboratory for comprehensive analysis
- Develop action plans based on analysis results
- Track trends over time to identify gradual changes in equipment condition
Acoustic emission testing for structural integrity assessment
Acoustic emission testing is a non-destructive technique used to assess the structural integrity of equipment and infrastructure. By detecting and analyzing sound waves produced by material deformation or cracking, maintenance teams can identify potential failures in pressure vessels, storage tanks, and piping systems. This method is particularly valuable for detecting minute flaws that may not be visible through other inspection techniques.
When implementing acoustic emission testing:
- Identify critical structures and components for monitoring
- Install acoustic sensors at strategic locations
- Establish baseline acoustic signatures during normal operation
- Configure alert systems for abnormal acoustic events
- Integrate acoustic data with other predictive maintenance techniques for comprehensive analysis
Developing a comprehensive maintenance schedule
Creating an effective maintenance schedule is crucial for balancing preventive and predictive maintenance activities with day-to-day operations. A well-designed schedule ensures that all equipment receives appropriate attention while minimizing disruptions to production. The key is to strike a balance between maintaining equipment reliability and optimizing resource utilization.
Balancing daily, weekly and monthly maintenance tasks
When developing a maintenance schedule, it's essential to categorize tasks based on their frequency and importance. Daily tasks might include equipment inspections, lubrication checks, and minor adjustments. Weekly tasks could involve more detailed inspections, filter changes, and performance tests. Monthly tasks might encompass comprehensive system checks, calibrations, and predictive maintenance activities.
Consider using a color-coded system or digital calendar to visualize the maintenance schedule. This approach helps maintenance teams quickly identify upcoming tasks and allocate resources accordingly. Regular review and adjustment of the schedule ensure that it remains aligned with evolving operational needs and equipment performance.
Integrating manufacturer recommendations into maintenance plans
Manufacturer recommendations provide valuable guidance for equipment maintenance. These recommendations are based on extensive testing and field experience, making them a reliable starting point for developing maintenance routines. However, it's important to adapt these recommendations to your specific operating conditions and usage patterns.
When integrating manufacturer recommendations:
- Review and document all manufacturer-specified maintenance tasks
- Assess the applicability of each task to your operating environment
- Adjust maintenance frequencies based on equipment criticality and usage
- Incorporate manufacturer-recommended spare parts into inventory management
- Stay updated on any revisions or updates to manufacturer guidelines
Adapting maintenance frequency based on equipment usage patterns
Equipment usage patterns can vary significantly, even within the same facility. Adapting maintenance frequencies to reflect actual usage ensures that resources are allocated efficiently. For example, a machine operating 24/7 may require more frequent maintenance than one used only during single shifts.
To optimize maintenance frequency:
- Implement equipment usage tracking systems
- Analyze historical maintenance data alongside usage patterns
- Adjust maintenance intervals based on actual operating hours or cycles
- Consider environmental factors that may impact equipment wear
- Regularly review and update maintenance frequencies to reflect changing conditions
Maintenance management software: streamlining routine procedures
In today's digital age, maintenance management software plays a crucial role in developing and executing effective maintenance routines. These powerful tools help organizations streamline workflows, track assets, manage work orders, and analyze maintenance data for continuous improvement.
Implementing CMMS solutions for work order tracking
Computerized Maintenance Management Systems (CMMS) are essential for efficient work order tracking and management. These systems allow maintenance teams to create, assign, and prioritize work orders, ensuring that all maintenance tasks are properly documented and executed. CMMS solutions also provide valuable insights into maintenance history, equipment performance, and resource utilization.
When implementing a CMMS:
- Choose a user-friendly interface to encourage adoption
- Customize workflows to match your organization's processes
- Integrate with existing systems for seamless data flow
- Provide comprehensive training to all users
- Regularly review and optimize system configurations
Utilizing mobile apps for real-time maintenance data collection
Mobile apps have revolutionized maintenance data collection by enabling technicians to input information directly from the field. These apps allow for real-time updates on work order status, equipment conditions, and parts usage. By eliminating paper-based processes and manual data entry, mobile apps improve data accuracy and reduce administrative overhead.
To maximize the benefits of mobile maintenance apps:
- Select apps compatible with your existing CMMS or EAM system
- Ensure robust wireless connectivity throughout your facility
- Implement secure authentication and data encryption measures
- Provide ruggedized devices suitable for industrial environments
- Regularly update apps and devices to access new features and security patches
Leveraging Asset Performance Management (APM) tools
Asset Performance Management (APM) tools take maintenance management to the next level by integrating data from multiple sources to provide a comprehensive view of asset health and performance. These advanced systems use machine learning algorithms to analyze historical data, predict future performance, and recommend optimal maintenance strategies.
When implementing APM tools:
- Identify key performance indicators (KPIs) for each asset class
- Integrate data from IoT sensors, CMMS, and other relevant systems
- Develop custom dashboards for different user roles
- Establish a process for reviewing and acting on APM insights
- Continuously refine predictive models based on new data and outcomes
Training and certifying maintenance personnel
Developing an effective maintenance routine relies heavily on the skills and knowledge of maintenance personnel. Investing in comprehensive training and certification programs ensures that your team has the expertise to implement and execute advanced maintenance strategies. A well-trained workforce can significantly improve maintenance efficiency, reduce errors, and enhance overall equipment reliability.
Consider implementing a multi-tiered training program that covers both general maintenance principles and equipment-specific skills. This approach allows for continuous skill development and creates career advancement opportunities within the maintenance team. Partnering with equipment manufacturers and industry associations can provide access to specialized training resources and certification programs.
To create a robust training and certification program:
- Conduct regular skills assessments to identify training needs
- Develop a structured curriculum covering both technical and soft skills
- Utilize a mix of classroom instruction, hands-on training, and e-learning modules
- Implement mentoring programs to facilitate knowledge transfer
- Recognize and reward employees who achieve certifications or demonstrate exceptional skills
Cost-benefit analysis of proactive vs. reactive maintenance approaches
Understanding the financial implications of different maintenance approaches is crucial for developing an effective maintenance routine. While reactive maintenance may seem less costly in the short term, it often leads to higher overall expenses due to emergency repairs, production losses, and shortened equipment lifespan. Proactive maintenance, including preventive and predictive strategies, typically requires higher upfront investments but can yield significant long-term savings.
To conduct a thorough cost-benefit analysis:
- Calculate the total cost of ownership for critical assets
- Analyze historical maintenance and repair costs
- Estimate potential savings from reduced downtime and extended equipment life
- Consider the impact on production quality and customer satisfaction
- Evaluate the return on investment for predictive maintenance technologies
By carefully weighing the costs and benefits of different maintenance approaches, organizations can make informed decisions about resource allocation and maintenance strategies. This analysis should be an ongoing process, with regular reviews to ensure that the chosen maintenance routine continues to deliver optimal results as business needs and technologies evolve.
Developing an effective maintenance routine is a complex but essential task for any organization relying on equipment and assets. By combining preventive and predictive maintenance strategies, leveraging advanced technologies, and investing in personnel development, businesses can create a robust maintenance program that enhances equipment reliability, reduces costs, and supports overall operational excellence. Regular evaluation and adaptation of maintenance routines ensure that they remain effective in the face of changing business needs and technological advancements.