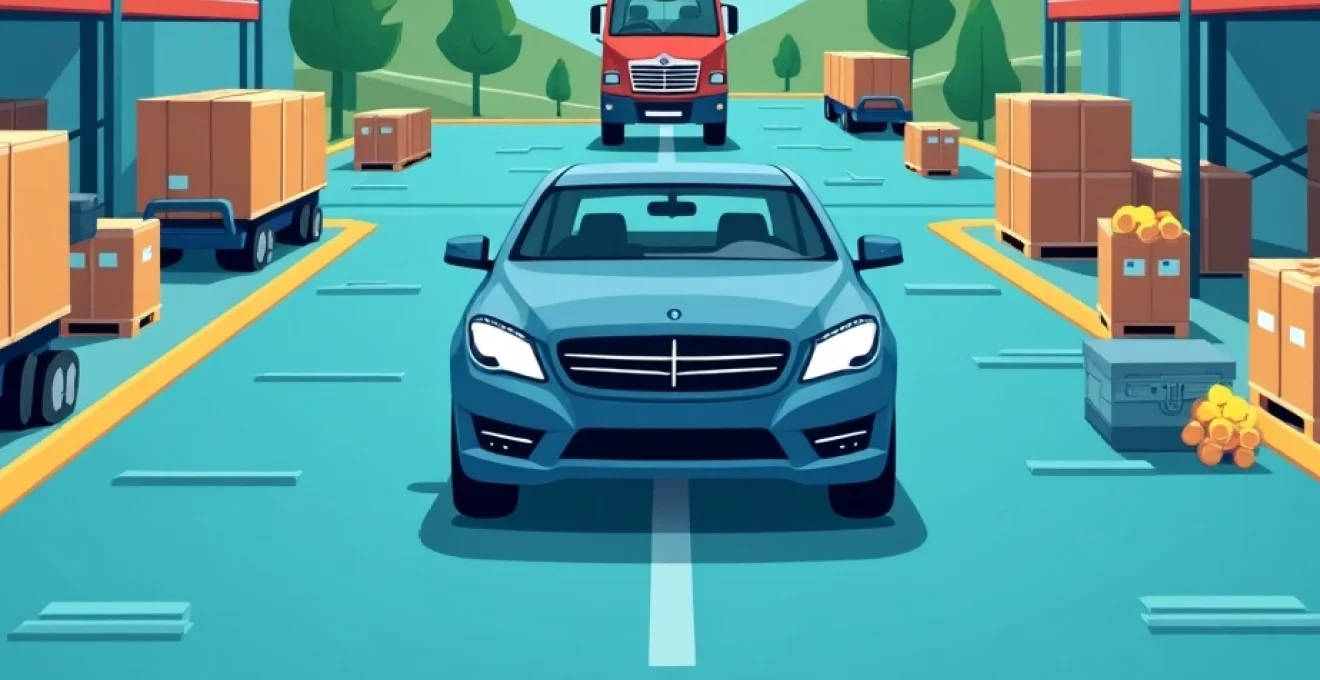
In today's fast-paced automotive industry, providing exceptional customer service is paramount for auto parts retailers and suppliers. Local sourcing has emerged as a powerful strategy to meet customer demands quickly and efficiently. By leveraging proximity to suppliers and implementing advanced inventory management techniques, businesses can significantly improve their responsiveness and overall customer satisfaction. This approach not only streamlines operations but also contributes to sustainability efforts and fosters stronger community relationships.
Local inventory management systems for auto parts retailers
Effective inventory management is the backbone of successful auto parts retailing. Local sourcing allows for more agile and responsive inventory control, enabling businesses to maintain optimal stock levels while minimizing excess inventory costs. By implementing sophisticated inventory management systems tailored to local market demands, retailers can ensure that the right parts are available at the right time, enhancing customer service and reducing wait times.
One of the key advantages of local inventory management is the ability to respond quickly to fluctuations in demand. This agility is particularly crucial in the auto parts industry, where vehicle models and repair trends can vary significantly by region. By closely monitoring local sales patterns and maintaining strong relationships with nearby suppliers, retailers can adjust their inventory in real-time, ensuring that popular items are always in stock while minimizing the risk of obsolescence for slower-moving parts.
Just-in-time sourcing strategies for automotive components
Just-In-Time (JIT) sourcing is a cornerstone of efficient local auto parts management. This strategy involves coordinating with local suppliers to deliver components precisely when they are needed, reducing storage costs and improving cash flow. By implementing JIT sourcing, auto parts retailers can maintain a lean inventory while still meeting customer demands promptly.
Real-time stock tracking with RFID technology
Radio-Frequency Identification (RFID) technology has revolutionized inventory tracking in the auto parts industry. By tagging individual components with RFID chips, retailers can monitor stock levels in real-time, automating the reordering process and minimizing human error. This level of precision in inventory management ensures that popular items are always available, enhancing customer satisfaction and reducing the likelihood of lost sales due to stockouts.
Implementing Kanban systems in auto parts warehouses
Kanban, a visual system for managing workflow, is particularly effective in auto parts warehouses. By using Kanban cards or electronic signals to trigger replenishment orders, warehouses can maintain optimal stock levels without overordering. This system aligns perfectly with local sourcing strategies, as the shorter lead times allow for more frequent, smaller deliveries, reducing the need for large storage spaces and improving overall operational efficiency.
Vendor-Managed Inventory (VMI) partnerships with local suppliers
Vendor-Managed Inventory partnerships represent a collaborative approach to inventory management. In this model, local suppliers take responsibility for maintaining agreed-upon stock levels at the retailer's location. This arrangement leverages the supplier's expertise and market insights, often resulting in more accurate demand forecasting and improved product availability. VMI partnerships can significantly enhance customer service by ensuring that popular parts are always in stock, reducing lead times, and minimizing the retailer's inventory management burden.
Demand forecasting algorithms for seasonal auto parts
Seasonal fluctuations in demand present a unique challenge for auto parts retailers. Advanced demand forecasting algorithms can analyze historical sales data, local weather patterns, and regional trends to predict future needs accurately. By incorporating these predictions into their local sourcing strategies, retailers can prepare for seasonal spikes in demand, such as increased sales of batteries in winter or air conditioning components in summer, ensuring they can meet customer needs without overstocking.
Enhancing customer experience through rapid parts availability
The ability to provide rapid parts availability is a significant competitive advantage in the auto parts industry. Local sourcing plays a crucial role in achieving this goal by reducing transportation times and enabling more flexible inventory management. When customers can quickly obtain the parts they need, it not only improves their immediate satisfaction but also builds long-term loyalty to the retailer.
Same-day delivery options for critical auto components
In situations where vehicle downtime is costly or inconvenient, same-day delivery of critical auto components can be a game-changer. Local sourcing makes this service possible by minimizing the distance between suppliers, retailers, and customers. By offering same-day delivery for urgent parts, retailers can position themselves as reliable partners for both individual car owners and professional mechanics, enhancing their reputation and customer service credentials.
In-store digital kiosks for parts lookup and ordering
Digital kiosks in auto parts stores provide customers with a self-service option for parts lookup and ordering. These kiosks can be connected to the local inventory management system, offering real-time information on part availability. If a specific component is not in stock, the kiosk can facilitate immediate ordering from a local supplier, often with the option for rapid delivery. This technology empowers customers, reduces wait times, and streamlines the purchasing process.
Mobile apps for Real-Time inventory checks and reservations
Mobile applications have become an essential tool for enhancing customer service in the auto parts industry. By developing apps that allow customers to check real-time inventory levels and reserve parts for pickup, retailers can offer unprecedented convenience. These apps can leverage local sourcing networks to provide accurate information on part availability and estimated delivery times, enabling customers to make informed decisions and plan their repairs more effectively.
Collaborative networks with local auto repair shops
Building strong relationships with local auto repair shops is a key strategy for auto parts retailers looking to enhance their customer service through local sourcing. By establishing collaborative networks, retailers can gain valuable insights into repair trends, common part failures, and emerging market demands. This information can be used to fine-tune inventory management and sourcing strategies, ensuring that the most needed parts are always readily available.
Collaborative networks also facilitate faster problem-solving when unusual or difficult-to-find parts are required. Through open communication channels, repair shops can quickly check availability across the network, reducing customer wait times and improving overall satisfaction. Additionally, these partnerships can lead to mutual referrals, benefiting both the parts retailer and the repair shop while providing customers with a more comprehensive service experience.
Quality control measures for locally sourced auto parts
While local sourcing offers numerous advantages in terms of speed and flexibility, maintaining high-quality standards is paramount. Implementing robust quality control measures ensures that locally sourced parts meet or exceed industry standards, protecting both the retailer's reputation and the customer's safety.
Implementing ISO/TS 16949 standards for automotive suppliers
The ISO/TS 16949 standard is specifically designed for the automotive industry and provides a comprehensive framework for quality management. By requiring local suppliers to adhere to these standards, retailers can ensure consistency in part quality and manufacturing processes. This commitment to quality enhances customer confidence and reduces the likelihood of returns or warranty claims due to defective parts.
Non-destructive testing techniques for component verification
Non-destructive testing (NDT) techniques play a crucial role in verifying the integrity of auto parts without damaging them. Methods such as ultrasonic testing, magnetic particle inspection, and radiography can detect internal flaws or structural weaknesses that might not be visible to the naked eye. By incorporating NDT into their quality control processes, local suppliers and retailers can provide customers with an additional layer of assurance regarding the reliability and safety of the parts they purchase.
Traceability systems for parts authentication and recall management
Implementing robust traceability systems is essential for managing product authenticity and potential recalls effectively. By assigning unique identifiers to each part and tracking them through the supply chain, retailers can quickly verify the origin and manufacturing details of any component. This capability is particularly valuable in the event of a recall, allowing for rapid identification of affected parts and efficient communication with customers. Traceability systems also help combat counterfeit parts, a significant concern in the automotive industry.
Environmental impact of local auto parts sourcing
Local sourcing of auto parts not only enhances customer service but also contributes significantly to reducing the environmental impact of the automotive supply chain. By minimizing transportation distances, local sourcing strategies can substantially decrease carbon emissions associated with parts distribution. This approach aligns with growing consumer awareness of environmental issues and can be a powerful differentiator for environmentally conscious customers.
Moreover, local sourcing often leads to more efficient inventory management, reducing waste from overstocking and obsolescence. Retailers can work closely with local suppliers to implement recycling programs for packaging materials and develop more sustainable practices throughout the supply chain. These initiatives not only benefit the environment but can also lead to cost savings and improved public perception of the business.
Local sourcing presents a multifaceted approach to enhancing customer service in the auto parts industry. By leveraging advanced inventory management systems, implementing just-in-time strategies, and fostering collaborative networks, retailers can significantly improve their responsiveness to customer needs. The integration of technology, from RFID tracking to mobile apps, further streamlines the purchasing process and enhances the overall customer experience. Quality control measures ensure that locally sourced parts meet rigorous standards, while environmental considerations add value for eco-conscious consumers. As the automotive industry continues to evolve, local sourcing will undoubtedly play an increasingly important role in meeting customer expectations and driving business success.